For about a year now I've been shy to try materials other than PLA; the "wisdom" seemed to suggest that you can't do anything interesting without a heated bed. Since I've enclosed my printer now in foam I'm making baby steps toward doing interesting things in this area.
Earlier today, I visited the Amazon Bookstore and saw one of these DOX things.
Coming home, I then immediately designed my own version for the Echo Dot. This initial version is just a passive stand from the standpoint of charging and mobility but with a twist. I've noticed that the speaker inside the Dot is directed downwards. So if you're going to add a stand, you need to have it acoustically invisible if you want to hear the output.
I've designed it like this, to direct the sound down and then forward out the hole in the front of the base's bottom. It should only add about 25mm to the height but should do a better job of directing the sound toward me.
Since I designed it to be so close to the actual diameter of the Echo Dot, I thought this might be a good time to use that GP3D FLEX Filament that I bought earlier. I was amazed at how flexible this stuff was when removing it from the box. My initial thought was to laugh and think "there's no way this is going to work".
Initially, it seemed to run fine at 195-degrees but I had some problems during the second layer. I started to lose the filament. I noticed that it was stuck in the PTFE tubing. So I pulled the filament so that the PTFE tubing was back from the bowden but it kept failing.
Version 2, I dropped the temperature down to 185-degrees and completely removed the PTFE tubing, adding a former raft to the top to direct the filament to the center of the gear teeth. I've rigged the second webcam so that I can watch the top of the bowden. It looks like this from the side:
Ultimately, this is the part I'm printing. I added supports but I'm not sure how this new filament will separate from itself. It was surreal trying to remove the failed earlier attempt from the bed and peeling it away (rather than popping it off).
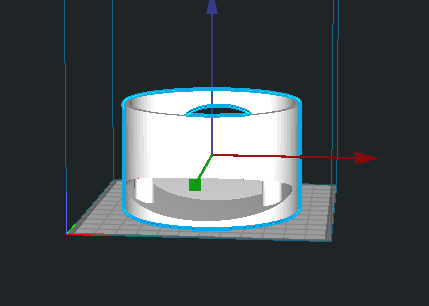
Wish me luck.
All I know about soft filament i.e EPA *nylon: is it should be printed with a .5 mm nozzle and very slowly. I have successfully printed it with a .35 at 10mmS on a MakerGear M2. Much faster than that it strips or bunches up in the drive..
Good luck!
I'm noticing that it's not being very consistent. I don't love changing nozzles so I can't imagine a single-extruder setup which happily allows me to go back and forth between materials with the ease that I'd like.
I've got the makings for a two-extruder setup but I haven't installed it yet.
I think I'd agree with your findings regarding the speed. I might be able to slow things way down with this 0.4mm nozzle but right now I have a delivery problem getting to the assembly itself: I can't use the PTFE tubing and I haven't got a solution yet for de-spooling that won't simply stretch the FLEX itself. My spool arrangement uses bearings and yet a full half-kilo roll just doesn't want to spin and the FLEX is too prone to stetching. I would almost need to create a two-bowden feed path to deliver this stuff.
That said, it's amazingly flexible. I would love to get the stuff to work.
I am guessing you printer is a delta? I was also told to rig a gravity feed for the real, have it above the printer so as not to have to pull..
1 Like
No, it's the standard design rather than a delta. (Robo C2) Maybe I can rig up something that sandwiches a wooden dowel within the foam layers at the top to feed it that way. Thanks for the idea.
Seems to work as designed. It fits perfectly, raises the Dot about 25mm off the table and directs the downward-facing sound toward the consumer. I'll need to use some sandpaper there where the supports just came off, though.
Oh, and finally (regarding the FLEX filament), I've decided that I will never EVER allow it to be the first layer of any project. It really does not want to come off the BuildTak.
I have had issues with EPA removing my Polyimide tape (kapton) and the cure is to lay down a nice coat of Elmers water base glue stick . Once complete, remove the build plate and run under water. The water dissolves the glue and the part comes off without damage to the surface. Still a pain but a work around.
Thanks, that sounds like it might work.
I do have some leftover tape squares. I suppose I could throw one of these down, do the glue thing and then see what happens.
I now have a rig at the top of the printer with a gravity feed, sans PTFE tubing. It seems to be stable enough and delivering the filament to the hotend.