You said it was having "gaps" in it. What kinds of gaps are you referring to ?
Cuz I tried swapping some parts on my Beta printer a few weeks ago so I could use a bowden setup, to get some of the mass off the rails, thinking that I'd be able to print faster if I could make Issac Newton happy, but, for some reason, all I ended up with was prints with what looked like swiss cheese holes in them
I tried turning up the flow and the feedrate (at one point, up to 300%) which did nothing, well, nothing helpful anyway, so I took out the bowden stuff, and went back to the (mostly) original setup
Somehow, something I did wasn't quite original, cuz, now the beta printer prints in CRAZY detail. It's as if I replaced the .4 nozzle with a .2 (which I didn't. I checked)
The green one here, is what I call swiss cheese
The black one is from the Alpha printer, which never tried to be a bowden, and the grey is the one that was bowden, then back to (mostly) stock Anet A8. It almost looks smooth
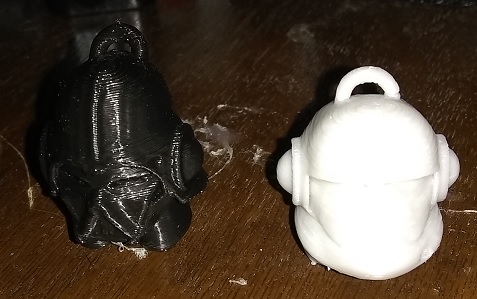
I did mostly the same upgrades to both Alpha and Beta, and the Cura settings are the same in both prints, but, the detail in Beta, as you can see, is much improved over Alpha (and no more swiss cheese)
Both of these were printed at .2 layer height, but, you would think that the grey was printed at .06 or something. I really wish I'd gotten the bowden to work that well